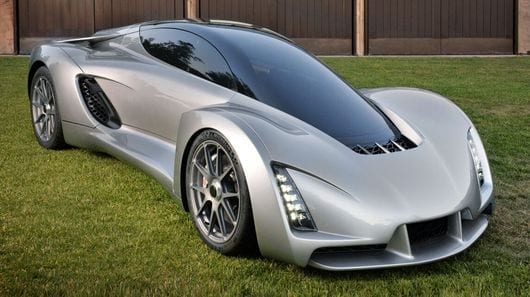
Automobiles have made great strides in recent years in becoming cleaner and greener, but according to Divergent Microfactories, they still have miles to go.
The problem, as the company sees it, is that while powertrains have become cleaner thanks to the use of alternative energy sources like battery power and fuel cells, manufacturing is dirtier than ever. The start-up puts forth a solution in the all-new Blade, which it calls “the world’s first 3D-printed supercar.”
Based in California, Divergent Microfactories was founded by Kevin Czinger, who also founded Coda Automotive. With Coda, he was focused on cleaning up the highways by promoting electric vehicle adoption. Coda’s electric car flopped, and the company filed for bankruptcy in 2013, emerging as the newly organized Coda Energy, a company that remains focused on energy storage for commercial and industrial applications.
Czinger has now turned his attention away from the roadways and toward the backend of the industry, working to create a cleaner, more efficient manufacturing paradigm based around 3D printing.
“A far greater percentage of a car’s total emissions come from the materials and energy required to manufacture it,” he explained during a keynote speech at last month’s O’Reilly Solid Conference. “How we make cars is actually a much bigger problem than how we fuel our cars.”
With visions of the hot rod building he did when he was younger, Czinger began formulating a simpler, less centralized concept of auto manufacturing based around a 3D-printed aluminum chassis joint he calls a node. The node is made by melting aluminum powder into form using a laser-based printing system. Individual nodes hold structural carbon fiber tubes together, building up a modular chassis like a sort of upsized children’s building kit.
Divergent says that its node-based chassis weighs some 90 percent less than an average car chassis and requires far less material and energy to produce. In fact, in introducing the concept, it carried the nodes and tubes for an entire chassis in a 120-liter (31.7 US gal) shoulder bag.
Divergent believes its 3D-printed nodes are analogous to the Arduinos that have opened up innovation within electronics, hiding technological complexity within an interface that is easy to work with. By using 3D-printed nodes, Divergent says that it can drastically cut down on the amount of space, time and investment required for automotive manufacturing. Once printed, the nodes allow a chassis to be constructed in a matter of minutes in a small, simple microfactory space. No longer will building a profitable car require the resources of a global corporation.
Read more: World’s first 3D-printed supercar aimed at shaking up the auto industry
The Latest on: 3D-printed car
[google_news title=”” keyword=”3D-printed car” num_posts=”10″ blurb_length=”0″ show_thumb=”left”]
via Google News
The Latest on: 3D-printed car
- Diesel Bikes, Abandoned Ships And UFOs In This Week's Beyond Cars Roundupon April 27, 2024 at 6:00 am
Diesel-powered motorcycles never really took off, for about one thousand reasons that make them worse than gas or electric bikes, but when have you ever cared about a vehicle being bad? You’re on ...
- 3D Printed Adapter Helps You Eat Chicken Nuggets On The Highwayon April 26, 2024 at 5:00 pm
If a smart little 3D-printed adapter can make mealtime easier and save some ... Heck, print in black and it’d look like a stock part of the car! You don’t have to like this simple adapter, but you can ...
- Czinger’s Latest 21C Hypercar Is The All-White Special ‘El Mirage’on April 25, 2024 at 8:22 am
The American marque dubs this 21C the El Mirage specification. It is the first example we’ve seen painted also entirely in white, a shade that helps to accentuate many of the car’s dramatic lines, ...
- University of Maine using giant 3D printer to build homeson April 23, 2024 at 2:22 pm
University of Maine, which boasts the world’s largest 3D printer, developed one even bigger that may one day create entire neighborhoods. The thermoplastic polymer printer was dubbed the “Factory of ...
- The Screw Bike Is a Bonkers Omnidirectional Self-Balancing E-Moto With 3D-Printed Wheelson April 23, 2024 at 2:13 pm
This unconventional-looking electric bike is the creation of James Bruton and can effortlessly move in any direction thanks to its Mecanum wheels ...
- Lenoir County Middle School students compete in miniature derby car raceon April 22, 2024 at 4:17 pm
On Monday, students from four different Lenoir County Middle Schools went at it to see which derby car reigned supreme. For more than a month now, students worked on ...
- 3D Printing To Lead Prototype Development for McLaren F1 Racingon April 22, 2024 at 9:08 am
McLaren Racing has fully embraced 3D printing for its prototype manufacturing process, as 3D printing has overtaken traditional methods.
- 3D-printed ‘ghost guns’ keep showing up at N.J. crime scenes, state probe findson April 17, 2024 at 4:18 pm
The State Commission of Investigation, an independent New Jersey government watchdog, held a hearing in Trenton on Tuesday as part of its probe into the proliferation of “ghost guns” and 3D-printable ...
- Formlabs launches Form 4 3D printer for prototyping to productionon April 17, 2024 at 1:01 pm
Formlabs announced the launch of its Form 4 and Form 4B 3D printers to help professionals go from prototype to production.
- Man accused of 3D printing universal mailbox keys in Harris County facing several fraud-related chargeson April 17, 2024 at 11:55 am
A Texas man accused of making 3D printed copies of counterfeit universal mail keys, known as arrow keys, has been indicted by a Harris County grand jury.
via Bing News