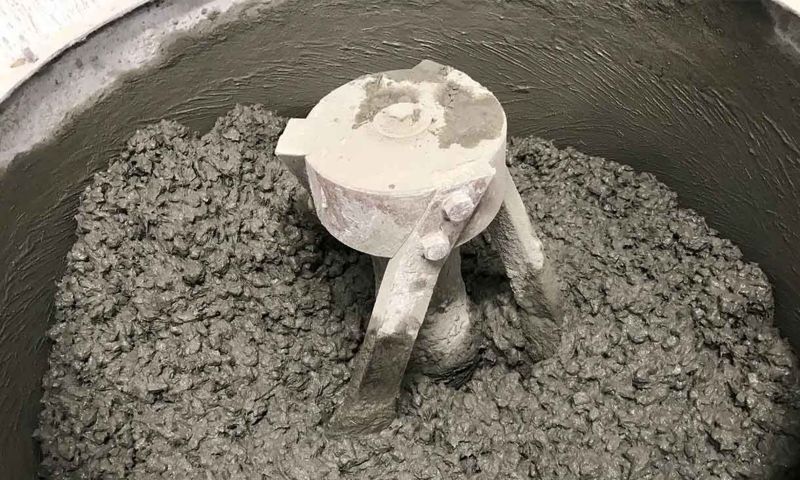
Concrete mixing using recycled tyre rubber particles for the complete replacement of traditional coarse aggregates.
Credit: Mohammad Islam, RMIT
Engineers have managed to replace 100% of conventional aggregates in concrete – such as gravel and crushed rock – with rubber from discarded tyres that meets building codes, promising a boost for the circular economy.
The team from RMIT University says the new greener and lighter concrete also promises to reduce manufacturing and transportation costs significantly.
Small amounts of rubber particles from tyres are already used to replace these concrete aggregates, but efforts to replace all of the aggregates with rubber have produced weak concretes that failed to meet the required standards – until now.
The study published in the Resources, Conservation & Recycling journal reveals a manufacturing process for structural lightweight concrete where the traditional coarse aggregates in the mix were completely replaced by rubber from used car tyres.
Lead author and PhD researcher from RMIT University’s School of Engineering, Mohammad Momeen Ul Islam, said the findings debunked a popular theory on what could be achieved with recycled rubber particles in concrete.
“We have demonstrated with our precise casting method that this decades-old perceived limitation on using large amounts of coarse rubber particles in concrete can now be overcome,” Islam said.
“The technique involves using newly designed casting moulds to compress the coarse rubber aggregate in fresh concrete that enhances the building material’s performance.”
This advance builds on the breakthrough invention of this technique by fellow RMIT University Engineers Professor Yufei Wu, Dr Syed Kazmi, Dr Muhammad Munir and Shenzhen University’s Professor Yingwu Zhou. Several national phase patent applications are now filed to continue protection of this technology.
Greener, cheaper and lighter building materials
Study co-author and team leader, Professor Jie Li, said this manufacturing process will unlock environmental and economic benefits.
“As a major portion of typical concrete is coarse aggregate, replacing all of this with used tyre rubber can significantly reduce the consumption of natural resources and also address the major environmental challenge of what to do with used tyres,” he said.
Used tyres in Australia cannot be exported, making new methods for recycling and reprocessing them locally increasingly important. About 1.2 billion waste tyres will be disposed of annually worldwide by 2030.
The greener and lighter concrete could also greatly reduce manufacturing and transportation costs, Li said.
“This would benefit a range of developments including low-cost housing projects in rural and remote parts of Australia and other countries around the world.”
Next steps
The team’s manufacturing process could be scaled up cost effectively within a precast concrete industrial setting in Australia and overseas, Islam said.
Following successful testing in the workshop, the team is now looking into reinforcing the concrete to see how it can work in structural elements.
Original Article: Concrete using recycled tyre rubber hits the road to a circular economy
More from: Royal Melbourne Institute of Technology | Shenzhen University
The Latest Updates from Bing News
Go deeper with Bing News on:
Green concrete
- Fairfield will close Perry's Green through summer to replace deteriorated seawall
Perry's Green will close from May to October as Fairfield installs a new concrete seawall to protect the Southport park from erosion and sinkholes.
- Green cement production is leaping ahead - and it could cut the carbon footprint of construction
Aside from water, concrete is the most-used material in the world, with about 14 billion cubic meters being used every year. Of that, 40% of that is used to build places for people to live. If you ...
- Rick Fox Combatting Climate Change With Green Concrete Company
Lakers great Rick Fox is going full force with his green concrete startup based in the Bahamas, Partanna Global Inc.
- NBA Legend Rick Fox's Next Act: Green Concrete Entrepreneur
But what set him on his green concrete journey was a nightmare. Fox grew up in the Bahamas. The azure-watered tourist destination was pummeled by Hurricane Dorian, one of the strongest hurricanes to ...
- Families of Texas bus crash victims sue concrete truck driver in 2nd lawsuit
In the second lawsuit since the deadly Texas bus crash three weeks ago, six families have sued the concrete truck driver and his company.
Go deeper with Bing News on:
Circular economy
- Investopia 2024 emphasises importance of driving new economy projects in AI, fintech, healthcare, environment
Investopia 2024 organised an all-encompassing strategic discussion, bringing together more than 105 speakers, including ministers, policymakers, leading investors, economic experts, and entrepreneurs ...
- Advancing India's Circular Economy: The Journey in E-Waste and Plastic Waste Management
Government entities, in collaboration with private enterprises, are establishing e-waste collection points and recycling facilities across the country.
- Circular Computing and Total IT Global Forge Partnership to Drive ESG Excellence in Enterprise IT
Circular Computing and Total IT Global partner to provide BSI-certified remanufactured laptops. These laptops perform as well as or better than new while reducing emissions and costs. Total IT ...
- Registration open for afternoon of circular economy webinars
Registration is now open for edie’s Circular Economy Action Sessions, two back-to-back webinars featuring experts and end-user businesses such as the Ellen MacArthur Foundation and BSI, to help ...
- Investing in the circular economy
The concept of a circular economy has gained prominence in recent years, embracing a regenerative system where products and materials are reduced, reused, and recycled, minimising waste and ...