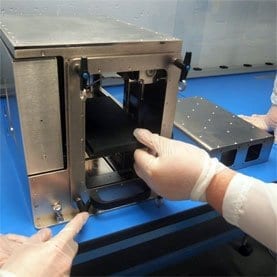
NASA has big plans for 3-D printing in space, where mined asteroid materials could resupply longer missions
The infamous NASA tool bag lost in space during a November 2008 International Space Station (ISS) maintenance mission left the crew with one less grease gun and no way to replace the missing tool. In a few years astronauts may be able to restock lost or damaged instruments by simply 3-D printing new ones.
NASA will test the feasibility of 3-D printing in a confined microgravity environment early next June when it sends a microwave-size printer to the ISS for a series of experiments producing plastic and composite parts and tools. If all goes well, the space agency plans to install a permanent ISS printer in 2015.
In the near term such a machine would let the ISS crew replicate odds and ends—plastic clips to anchor cargo, for example—without having to wait for the next resupply mission. Further in the future the space agency imagines a day when raw materials mined from asteroids could be delivered to a spacecraft or orbital lab and used as 3-D printing fodder. The ability to resupply far from Earth would give such a vessel the ability to carry out longer, deep-space missions, assuming myriad other sticking points are worked out—fuel, food and radiation exposure among them.
Test run
First things first: Astronauts will install the test 3-D printer—built by a company called Made in Space—in the ISS’s Microgravity Science Glovebox, an enclosed 255-liter work space located in the European Space Agency’s Columbus laboratory module. ESA developed the work space to allow terrestrial scientists from different disciplines carry out experiments in space, aided by ISS crew members via real-time data links and video. The work space is sealed and held at a negative pressure to enable the crew to manipulate experimental hardware and samples without the danger of small parts, particulates, fluids or gases escaping into the open laboratory module.
Made in Space’s printer builds objects by first heating a thermoplastic filament and then using an extrusion head to deposit the softened material according to a blueprint dictated by a computer-aided design (CAD) file. This printing technique—commonly used by inventors for quickly prototyping their designs—creates items from the bottom up, depositing materials in layers as thin as 0.04 millimeter.
3-D printers are generally designed to take advantage of gravity and surface tension to help form layers without air bubbles or other imperfections that weaken the finished product. “In the presence of microgravity all the components of a 3-D printer begin to float around, and even fractions of a millimeter of float can be detrimental to a print,” says Made in Space chief technology officer Jason Dunn. Without going into specifics—for competitive reasons—Dunn says that his company has developed “the first 3-D printer that is essentially gravity independent.”
The Latest Bing News on:
3-D Printing in Microgravity
- Global 3D Printed Prosthetics Industry is expected to reach US$3.5 Billion, growing at an 8% annual pace By 2033 | FMIon April 26, 2024 at 5:58 am
The Global 3D Printed Prosthetics Industry is poised for significant growth, driven by rising healthcare spending, technological advancements, and increasing demand for customized prosthetic solutions ...
- Serra High space team seeks to turn school into science destinationon April 25, 2024 at 3:00 am
The Serra High School space team's second out-of-earth experiment was launched aboard the SpaceX Falcon 9 CRS-30 Rocket from Florida's Kennedy Space Center on March 21 and docked with the ...
- Scientists create method of '3D-printing realistic robot fingers'on April 23, 2024 at 7:04 am
Scientists from the Swiss Federal Institute of Technology in Lausanne have created a method of 3 D-printing fingers for robots or prosthetics with similar properties to those of human flesh. A team of ...
- I Tried 3D Printing a Photo, Here's How It Wenton April 23, 2024 at 4:00 am
True lithophanes are porcelain pieces that have designs pressed into them when the porcelain is soft. Then, when held up to a light, the image becomes visible. The different thicknesses of the ...
- 'The 3D printing market in China is theoretically huge, but it is still catching up to 'North America & Europe' - Ryan Liuon April 22, 2024 at 1:43 am
Chinese manufacturers still have some catching up to do when it comes to the application on additive manufacturing, according to Ryan Liu.
- An ink for 3D-printing flexible devices without mechanical jointson April 19, 2024 at 4:34 pm
Researchers are targeting the next generation of soft actuators and robots with an elastomer-based ink for 3D printing objects with locally changing mechanical properties, eliminating the need for ...
- New Plastic Coating Discovery Gives Greater Functionality to 3D Printingon April 18, 2024 at 1:34 pm
The anti-mold and anti-fungal coating can easily be incorporated into current commercial 3D printing processes ...
- Stratasys (SSYS) Unveils Direct-to-Garment 3D Printing Solutionon April 18, 2024 at 2:37 am
Stratasys SSYS has launched its Direct-to-Garment (D2G) solution for the J850 TechStyle 3D printer in a groundbreaking move that combines personalized fashion with sustainability. This innovative ...
- Startup Looking to Launch Stadium-Sized Space Habitats on SpaceXon April 12, 2024 at 10:47 am
Space Balloon Space startup Max Space is hopping to launch expandable, "stadium-sized" habitats into the Earth's orbit on board a SpaceX rocket as soon as 2026. The nascent startup's goal is ...
The Latest Google Headlines on:
3-D Printing in Microgravity
[google_news title=”” keyword=”3-D Printing in Microgravity” num_posts=”10″ blurb_length=”0″ show_thumb=”left”]
The Latest Bing News on:
3-D printing in space
- 3D printers are helping surgeons create custom cranial implantson April 26, 2024 at 11:28 am
I know that if I suffer a severe injury, especially to my skull, all I really need is a 3D printer. Now that I’m in my 40s, I’m more acutely aware of the inherent risk of injury in normal, everyday ...
- World's biggest 3D printer whirs into actionon April 26, 2024 at 7:09 am
A giant 3D printer, which is big enough to make a house, has been unveiled at the University of Maine. The university says it has beaten its own record for the world's largest polymer 3D printer - ...
- INDO-MIM taps 3D printing in precision manufacturingon April 25, 2024 at 6:27 pm
The precision metal parts manufacturer is using HP’s Metal Jet S100 printers to produce components using metal powder for the automotive, healthcare and other industries ...
- Serra High space team seeks to turn school into science destinationon April 25, 2024 at 3:00 am
The Serra High School space team's second out-of-earth experiment was launched aboard the SpaceX Falcon 9 CRS-30 Rocket from Florida's Kennedy Space Center on March 21 and docked with the ...
- The world’s largest 3D printer is at a university in Maine. It just unveiled an even bigger oneon April 24, 2024 at 2:45 pm
The university that boasts the world’s largest 3D printer developed one even bigger. And it’s poised to help tackle one of America’s biggest problems of all.
- For science: Astronaut gets ultrasounds, other measurements in spaceon April 24, 2024 at 6:20 am
NASA astronaut and University of San Diego alumnus Matt Dominick, aboard the International Space Station As a flight engineer and laboratory technician, Dominick and his colleagues conduct scientific ...
- University of Maine unveils larger, faster 3D printeron April 23, 2024 at 7:37 pm
The University of Maine today unveiled a new large-scale 3D printer, and university officials said it will allow researchers to create bigger projects in less time. The new printer, called Factory of ...
- From Orbit to Object: Transforming Space Probe Paths into 3D Printson April 23, 2024 at 9:03 am
A new research paper proposes a method to use interplanetary space probe trajectories as a method to generate unique 3D printable designs.
- 3D printing startup secures partnership with HP shortly after launchingon April 19, 2024 at 9:30 am
The founders of a new additive manufacturing startup in West Michigan are leveraging a partnership with multinational I.T. firm HP Inc. to innovate in the 3D printing space.
- Reuters Videoon April 17, 2024 at 9:13 am
Reuters, the news and media division of Thomson Reuters, is the world’s largest multimedia news provider, reaching billions of people worldwide every day. Reuters provides business, financial, ...
The Latest Google Headlines on:
3-D printing in space
[google_news title=”” keyword=”3-D printing in space” num_posts=”10″ blurb_length=”0″ show_thumb=”left”]